3D Printing with PEEK, PEKK, & ULTEM™
Join AON3D's 3D printing application and materials experts for a 30-minute session that covers all the key information
3D printed parts will be taken to new heights onboard Astrobotic’s Peregine Lunar Lander. Along with marking the first time that an American lunar lander will return to the moon since 1972, an important milestone is underway – demonstrating that additive manufacturing (AM) can be used beyond prototyping, with the development of high-performance components that can withstand the extreme conditions in space.
While most businesses are not sending parts to space, this achievement illustrates the viability of AM components for direct end-use applications in the most demanding environments. This case study illustrates how a former Google Lunar X Prize contender is leveraging AM to cut costs and rapidly develop the world’s first commercial lunar lander.
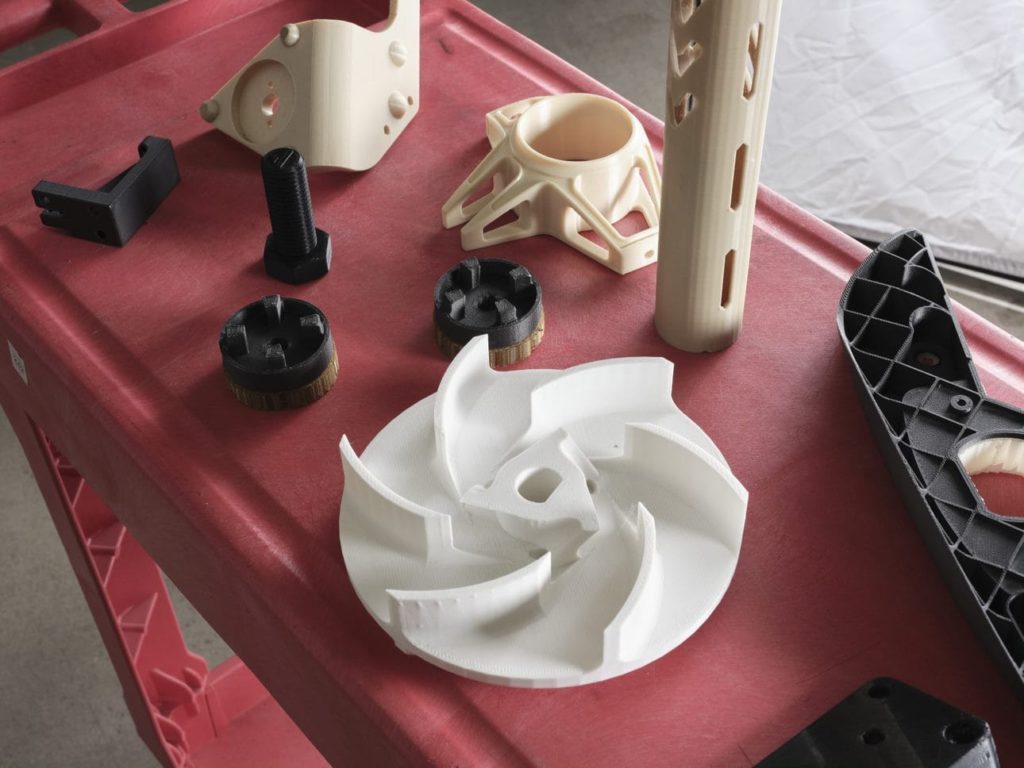
The Company and Mission
Astrobotic is an American privately held company that specializes in making space missions feasible and more affordable for science, exploration, and commerce. They achieve this by developing advanced navigation, operation, and computing systems for spacecraft and their fleet of lunar lander will soon deliver payloads to the Moon. Funded by several government and private industries, Astrobotic aims to make space more accessible to the world starting with Peregine Mission One (PM1). PM1’s lander will be the world’s first commercial lunar lander carrying scientific instruments, technologies, and thousands of individuals mementos to the moon through DHL’s MoonBox program.
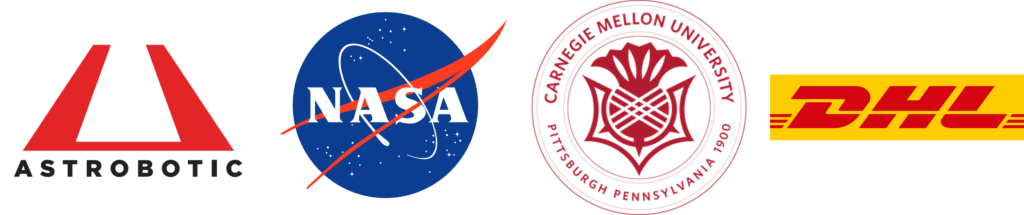
The Challenge
Cost
Aerospace manufacturing is an expensive process due to several factors, one being the buy-to-fly ratio; the mass of raw material required for the unit mass of final part. This ratio can approach 20:1 for complex aerospace parts, meaning 20 kgs of raw material is required for 1kg of a flight ready component. As a result, subtractive manufacturing methods can incur large capital requirements to create complex geometries and require design for manufacturing. Astrobotic needed a solution which provided low initial capital expenditure, a sustainable total cost of ownership and greater freedom of design.
Additionally, while metals offer high mechanical strength and stiffness, their high density contributes to an increase in the overall weight of the launched payload. With the price tag of around $1.2M to send a kilogram to the lunar surface, alternative material choices would have to be considered. Certain polymers offer a decrease in component weight and launch costs while maintaining a strength-to-weight ratio comparable to that of metals.
Time
As a small business with limited capital and tight deadlines, Astrobotic did not have the bandwidth to purchase expensive machinery or outsource their production due to the large lead times. They required a manufacturing technology capable of rapid prototyping to facilitate fast design iterations and producing end-use parts to meet their mission targets.
Engineering
The selected polymers for space need to have good thermal stability to survive the variations in temperature and good physically stability in a vacuum. Polymers can outgas in a vacuum which is detrimental to the performance of the component due to mass loss [1]. These materials can also react with atomic oxygen, resulting in degradation and erosion of surfaces in space [2].
So which polymers are suitable for the conditions in space and what are the design considerations? The next section of this case study on 3D printing for space will cover why Astrobotic selected additive manufacturing and the material selection criteria.
The Solution
Meeting Business Requirements
To meet their cost, time, and engineering requirements, Astrobotic turned to the AON M2+. From the available printers in the market, the M2+ has the best return on investment (ROI), features an open materials system, can print low and high temperature polymers, sustains low operating costs, and produces parts with high reliability and repeatability.
Replacing Metals and Developing End-use Parts
PEEK, PEKK and ULTEM were the material candidates that Astrobotic considered for their lunar lander. These high strength polymers are capable of resisting the extreme temperature differentials in space, maintain mechanical integrity in vacuum, and outgas at an acceptable rate [1, 3]. The densities of these polymers are less than 50% of aluminum’s density, so the weight was effectively reduced by half when replacing flight components made of aluminum or similar metals.
Astrobotic also required a system that was capable of rapid prototyping with more economical materials. The decision to choose the AON M2+ was backed by the printer’s capability to use low-cost materials for rapid prototyping as well as to print high temperature polymers for direct end-use parts with a large build volume (450 x 450 x 640mm). Additionally, a dual extrusion system ensured multi-material printing capabilities and dissolvable support materials to reduce post processing time. The costs associated with post processing and assembly were in-turn mitigated given the ability to directly produce flight-ready components.
The video below highlights the key takeaways from this case study of 3D printing for space and details the experience from the perspective of Astrobotic.
The Parts
Prototypes
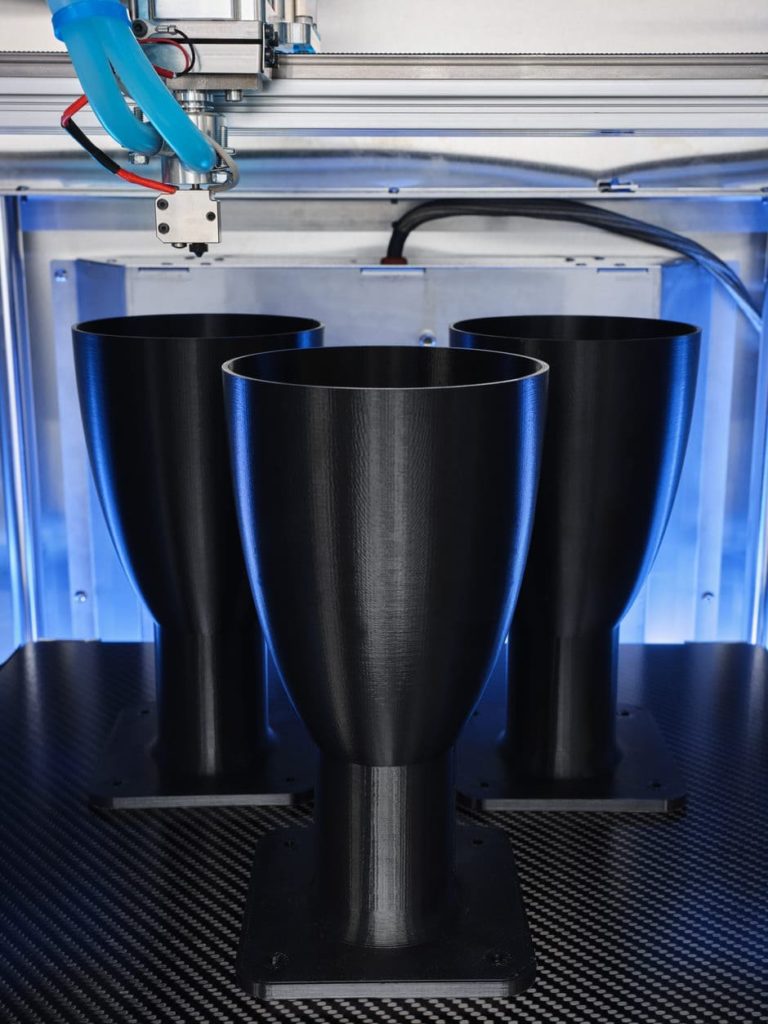
Full-scale avionics boxes, relays, bus bars, connectors, and other mockups were printed in-house saving weeks in lead times at an order of a magnitude cheaper on a per part basis.
Electrical System Components
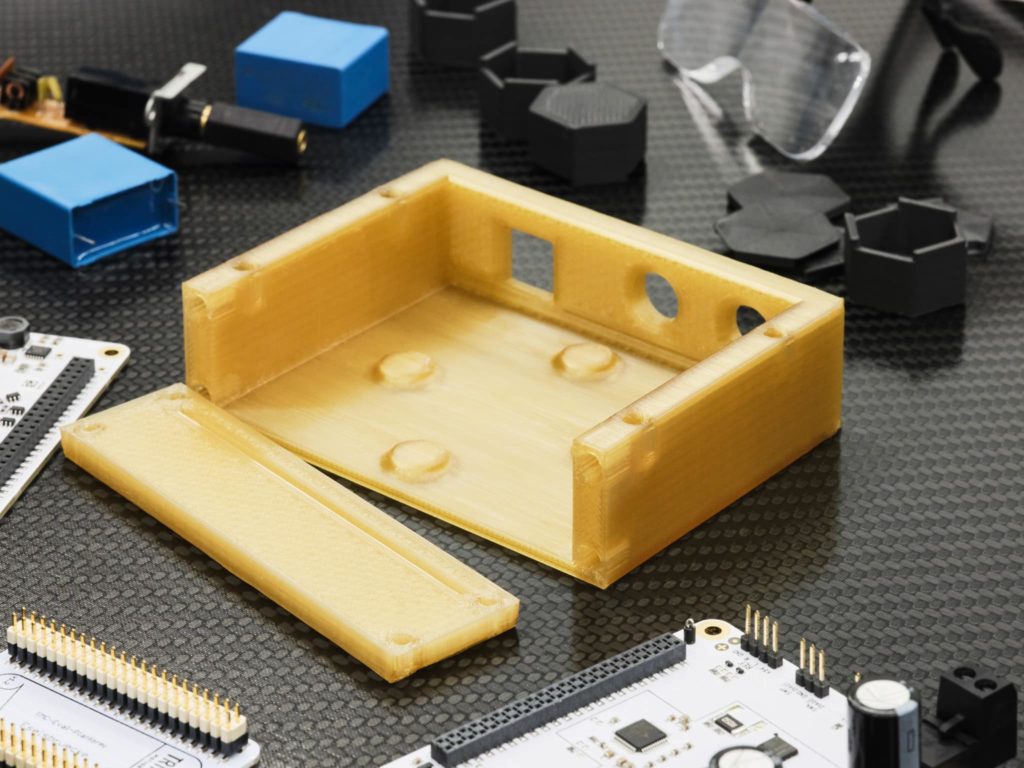
Hundreds of fixtures and brackets replace metal components, ensuring avionics and electrical system integrity while reducing vehicle mass, enabling design freedom, and speeding production. Peregrine’s avionics perform all command and data handling for the lander.
MoonBoxes
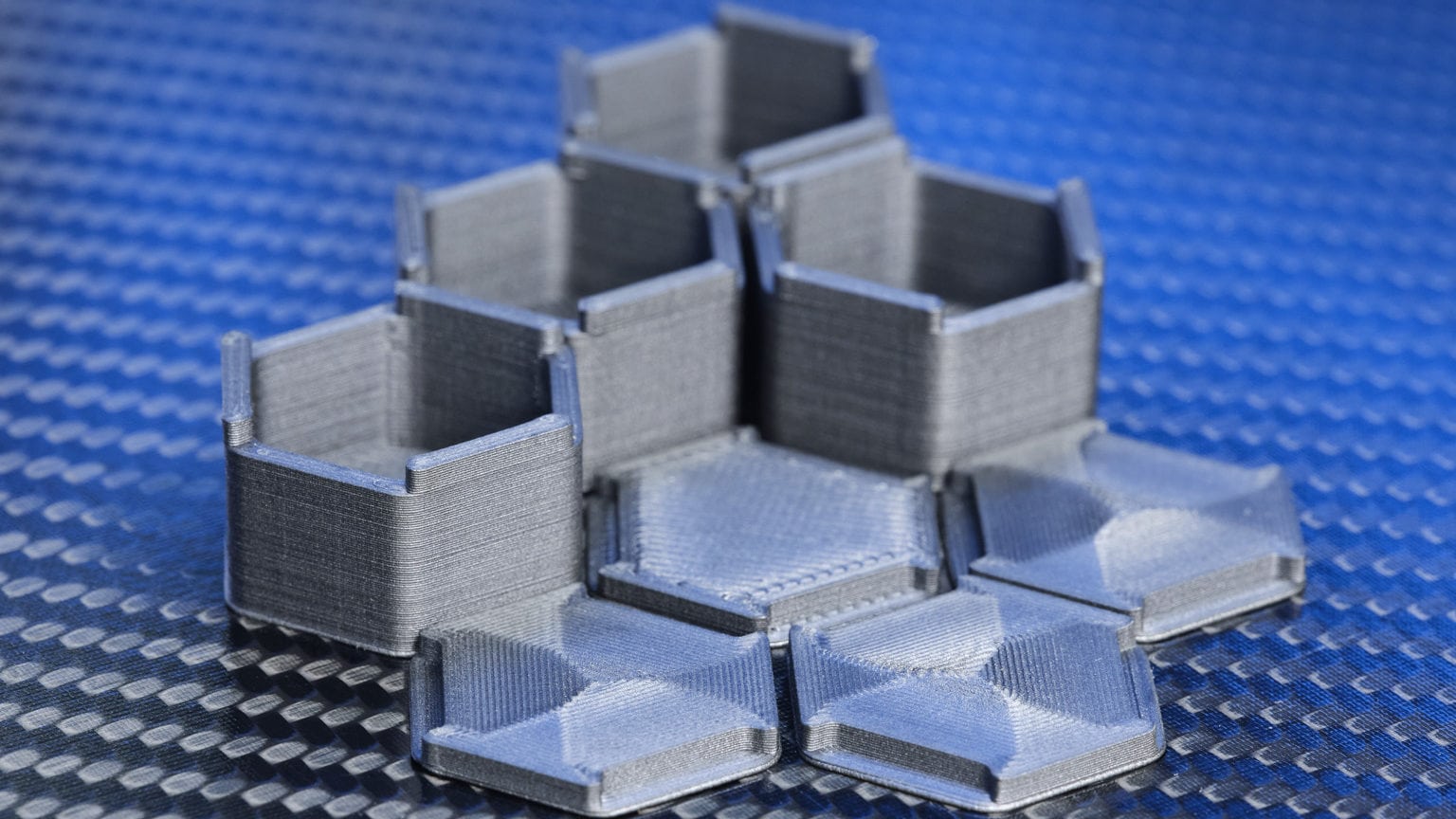
The world’s first commercial payloads delivered to the Moon’s surface, including two minted cryptocurrencies, will be packaged in 3D printed boxes made from high-performance materials to reduce mass.
References
[1] J. Knipple, “Outgassing Data for Selecting Spacecraft Materials,” National Aeronautics and Space Administration, 2 April 2008. [Online]. Available: https://outgassing.nasa.gov/. [Accessed 20 September 2021].
[2] M. M. Finckenor and K. K. d. Groh, International Space Station (ISS) Researcher’s Guide, NASA ISS Program Science Office, 2020.
[3] CRAFTECH INDUSTRIES, INC., “Low Outgassing Materials,” [Online]. Available: https://www.craftechind.com/app/uploads/low-outgassing-materials-for-website.pdf. [Accessed 17 09 2021].
Achieve New Levels of Part Performance & Throughput
3D print the world's highest performance polymers - bigger, faster, and stronger than ever.