3D Printing with PEEK, PEKK, & ULTEM™
Join AON3D's 3D printing application and materials experts for a 30-minute session that covers all the key information
Introduction
As an essential part of nearly any manufacturing process, tooling can significantly improve a production line’s throughput and repeatability while reducing cost per part. With advancements in high performance materials, additive manufacturing (AM) is now being applied in some of the most demanding end-use tooling applications. Compared to conventional manufacturing methods, AM provides greater design complexity, enables assembly consolidation, and dramatically reduces tooling costs and lead times.
This guide will help manufacturers and engineers discover potential tooling applications with industrial 3D printing and high performance polymers. In addition, find material recommendations, cost/time savings, and tips to apply AM in your processes.
Taking Tooling to the Next Level with High Performance Polymers
High performance polymers, such as PEEK, PEKK, and PEI, are a group of thermoplastics that exhibit extreme mechanical, thermal (up to 260°C), and chemical properties. Sometimes referred to as technopolymers, or metal replacement polymers, these materials redefine how additive manufacturing can be applied in tooling applications including welding fixtures, high temperature layups, metal forming dies, and more. It should be noted that 3D printing these materials requires a printer with high temperature extruders (>320°C) and a precision-controlled, actively heated build chamber (>130°C), such as the AON M2+.
Tooling Applications List
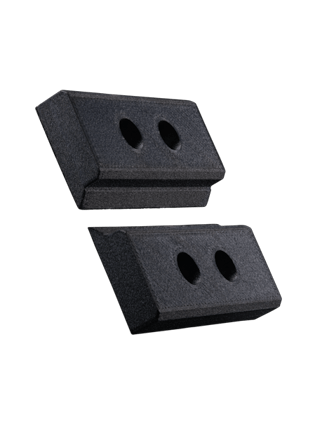
Jigs and Fixtures
Improve production efficiency and worker ergonomics while reducing costs and lead times with custom 3D printed jigs and fixtures. Threaded inserts, drill bushings, and hold-down clamps can easily be added to 3D printed parts to cater to various manufacturing applications. In addition, use TPUs to create workholding devices for irregularly shaped parts, ESD materials for PCB applications, and high performance materials for high heat, wear, and strength applications.
Applications | Drill Guides, Assembly Jigs, Inspection Jigs, Template Jigs, Workholding Fixtures, and more. |
Materials | ABS, ASA, CF Nylon, TPU, PEEK, PEKK, PEI, ESD Composites |
Average lead time savings | 60% – 90% |
Average cost savings | 80% – 90% |
Tips | Open material and dual extrusion 3D printers provide greater flexibility for tooling applications. |
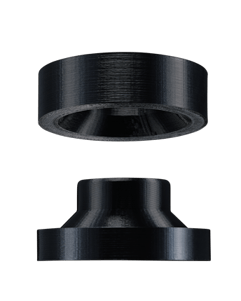
Metal Forming
Create same-day custom press brake dies, bending dies, or form blocks for hydroforming applications. Additive manufacturing provides a fast, low-cost solution for short- to medium-run metal forming and concept validation with up to 13 gauge aluminum, 14 gauge stainless steel, or 19 gauge titanium.
Applications | Dies, Form Blocks |
Materials | ABS, PC, PEEK, PEKK, PEI |
Average lead time savings | 60% – 80% |
Average cost savings | 55% – 90% |
Tips | High performance materials can be suitable for hydroforming up to 10,000 psi (69 MPa) and a maximum draw depth of 3in. Use a high infill percentage and increase your dies’ wall thickness to form thicker gauge metals. Avoid using carbon fiber filled materials for press brake dies, as they may create static electricity that can short press brakes. |
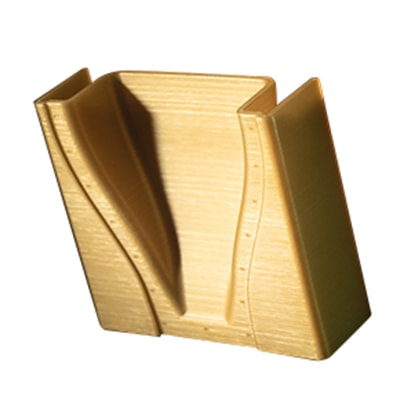
Composite Tooling
3D print high strength, high heat layup tooling (PEEK, PEKK) with a low coefficient of thermal expansion (CTE) for autoclave cured resins or use affordable, low-temperature commodity polymers (PC, PETG) for room temperature curing applications. Alternatively, high strength (up to 101 psi) and high heat (up to 130°C) water-soluble materials can be used to create complex sacrificial cores.
Applications | Layup Tooling, Soluble Cores |
Materials | PC, PETG, CF PEEK, CF PEKK, AquaSys® 180 |
Average lead time savings | 50% – 85% |
Average cost savings | 75% – 95% |
Tips | Use chopped carbon fiber-filled materials to further reduce your mold’s coefficient of thermal expansion. |
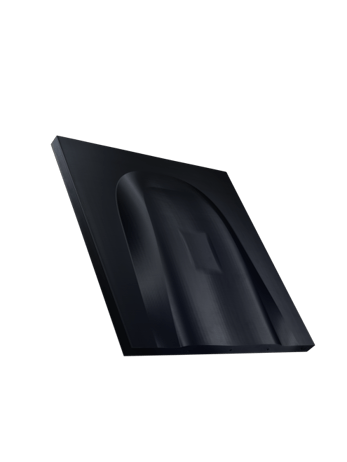
Thermoforming Tools
Create fast, low-cost molds for heavy and thin gauge vacuum forming applications utilizing ABS, Acrylic, HDPE, KYDEX®, PET, PVC, and more. Using engineering-grade or high performance polymers, molds possess ample heat deflection and durability to withstand 1000+ hits.
Applications | Vacuum Forming |
Materials | CF Nylon, PC, CF PC, PEI |
Average lead time savings | 50%+ |
Average cost savings | 70% – 80% |
Tips | Use chopped carbon fiber-filled materials, such as CF Nylon, to further reduce your mold’s coefficient of thermal expansion. |
Trim Tooling
Create custom workholding fixtures for post-processing metal, carbon fiber, and thermoplastic parts. High performance 3D printing materials are high strength and possess extreme heat and wear resistance properties, making them suitable for CNC, waterjet, and other trimming processes.
Applications | Trim tools for CNC, Waterjet, and more. |
Materials | CF ABS, PC, PEKK, PEI |
Tips | Use high performance polymers for dimensional stability in high heat applications. |
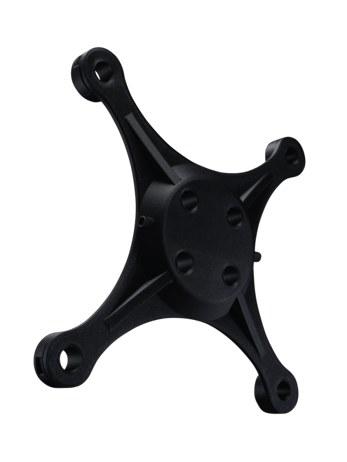
Automation Tools
Create custom lightweight/low mass end of arm tooling (EOAT). 3D printing offers several advantages over conventional manufacturing, including higher design complexity with added costs, assembly consolidation, and integration of vacuum channels within end effectors.
Applications | End of Arm Tooling |
Materials | ABS, ASA, PC, CF Nylon, PEI |
Average lead time savings | 90%+ |
Average cost savings | 95%+ |
About AON3D
AON3D is an industrial 3D printer manufacturer specializing in high performance polymers. The AON M2+ is large (450 x 450 x 565 mm), open material, and high temperature 3D printer designed to give manufacturers the flexibility needed to produce industrial-grade parts for some of the world’s most demanding applications. Contact our additive manufacturing specialists to learn how your business can implement industrial 3D printing in your manufacturing processes.
Achieve New Levels of Part Performance & Throughput
3D print the world's highest performance polymers - bigger, faster, and stronger than ever.