3D Printing with PEEK, PEKK, & ULTEM™
Join AON3D's 3D printing application and materials experts for a 30-minute session that covers all the key information
PEEK and PEKK are two of the highest performance polymers that are printable through fused filament fabrication (FFF). But what gives rise to their unique properties and what differentiates the two materials in terms of performance and printability? Here we compare the chemical structures to break down why PEKK is easier to print and the recommended printer settings to manufacturing high quality parts.
Why print with PEEK and PEKK?
An immediate question that you may ask is why even consider PEEK and PEKK for your application? Over recent years, these polymers have garnered popularity due to their high mechanical strength, rigidity, insulative, chemical and temperature resistant properties. In some cases, these materials can match the mechanical properties of aluminum alloys while being 40% lighter. PEEK and PEKK are resistant to fires, acids or hydrocarbons which allows applications in the aerospace, automotive, and railway industry.
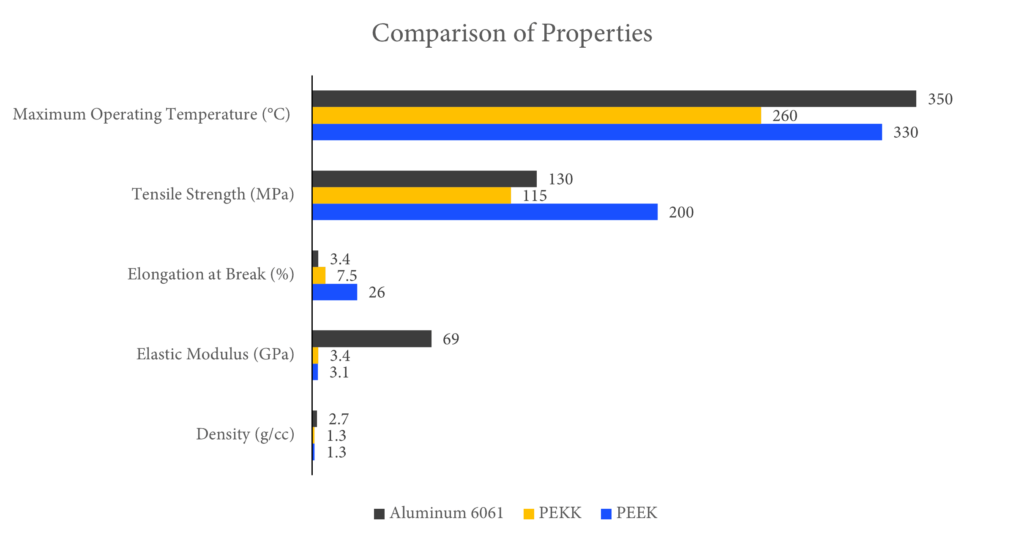
Structural similarities of PEEK and PEKK
PEEK and PEKK are both members of the PAEK family, a group of semi-crystalline polymers. In our previous article on the crystallinity of PEEK, we discussed how semi-crystalline polymers are made up of a crystalline phase and an amorphous phase. What we found is that the crystalline phase occupies less space because the polymer chains are more tightly packed and organized compared to the amorphous phase.
During the FFF process, crystallization takes place as the molten polymer is deposited. Over time, the crystalline phase begins to grow where polymer chains begin to fold and organize themselves into a lamellar structure. The lamellar crystals grows radially as spherulites, shown as the circular structures below. The noodle-like amorphous phase shown in white surrounds the nucleating crystalline phases. Not all polymer chains are able to organize themselves which is why we have an upper limit on the crystallinity of polymers, usually around 30-40% for PEEK.
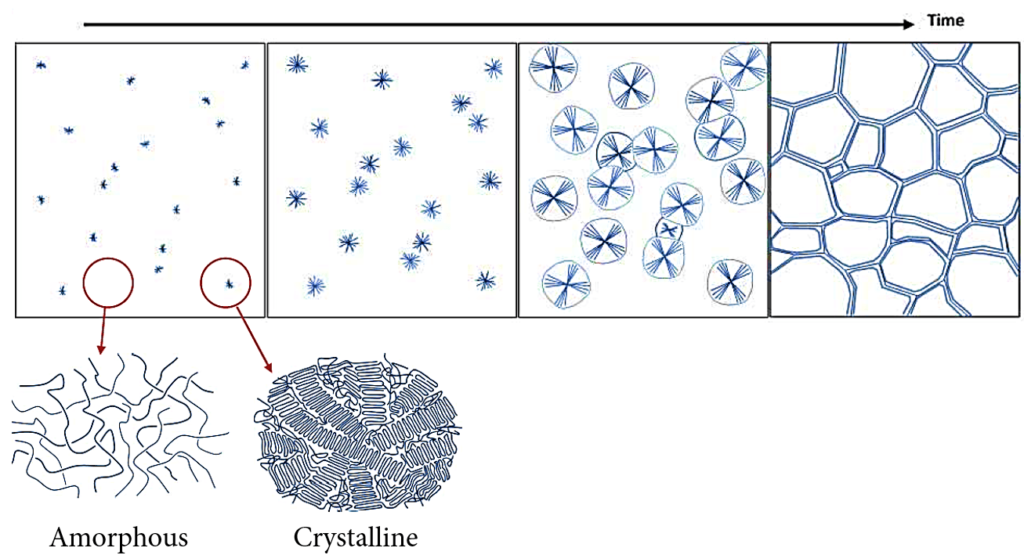
Now why is this important? The rate at which these crystals form has a profound effect on polymers during the FFF process. Let’s explore this by demonstrating why PEEK is so challenging to print.
The challenges of printing PEEK
When processing semi-crystalline polymers like PEEK, it’s important to know when crystallization occurs. As PEEK is extruded from the nozzle, the temperature drops below the melting point (343°C) and the polymer begins to solidify. Crystallization occurs between the melting point and the glass transition temperature (143°C). You can see the range of temperature in the graph below with the crystallization half-time – how long it takes for the polymer to achieve half of its maximum crystallization.
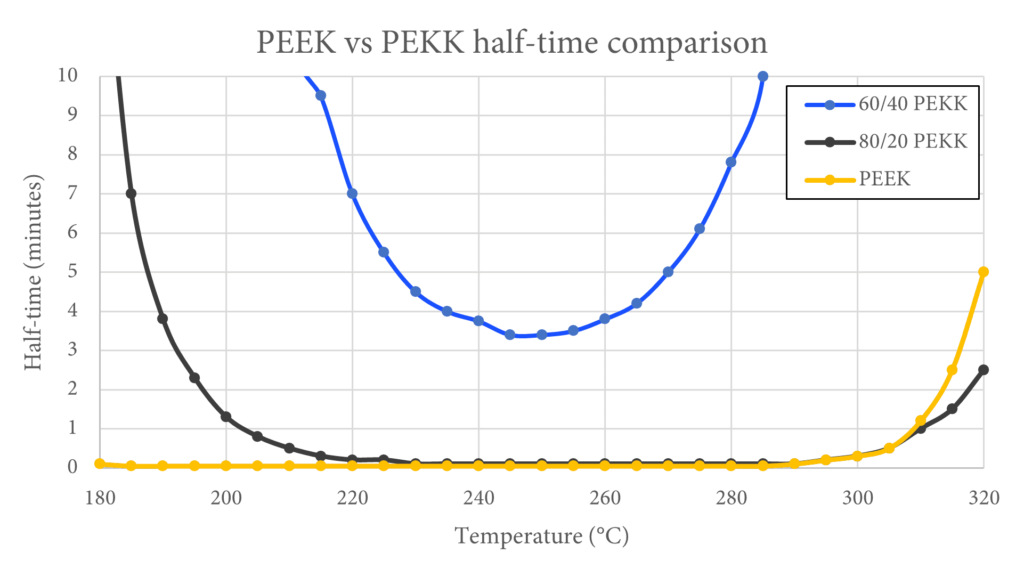
PEEK crystallizes just seconds after deposition for a wide range of temperatures. The rapid formation of the crystalline phase shrinks the polymer almost immediately, which is why we see warping in printed PEEK. When printing large geometries, the deposited PEEK will cool relative to the newly deposited layer. The cooled layers will contract which induces residual stress and warpage in the overall structure.
This is why materials scientists have spent resources developing more advanced materials like PEKK to improve the printability of high-performance polymers. So, lets understand why PEKK is easy to print.
Why PEKK is easy to print
A majority of polymers are made of a single repeating chemical structure. PEKK is a co-polymer, made up of two repeating chemical units. In the image below you will find one of the two stereoisomers (chemical structures) in PEKK along with PEEK for comparison. While more costly to produce, the benefits of co-polymers are that the ratio of the two chemical structures in PEKK can be controlled to influence bulk material properties. In other words, the rate of crystallization can be controlled by changing this ratio. In the graph above you will notice a few ratios for PEKK that have been plotted. For example, a 60/40 co-polymer ratio has a half-time around 3.5 minutes at 250°C.
PEEK
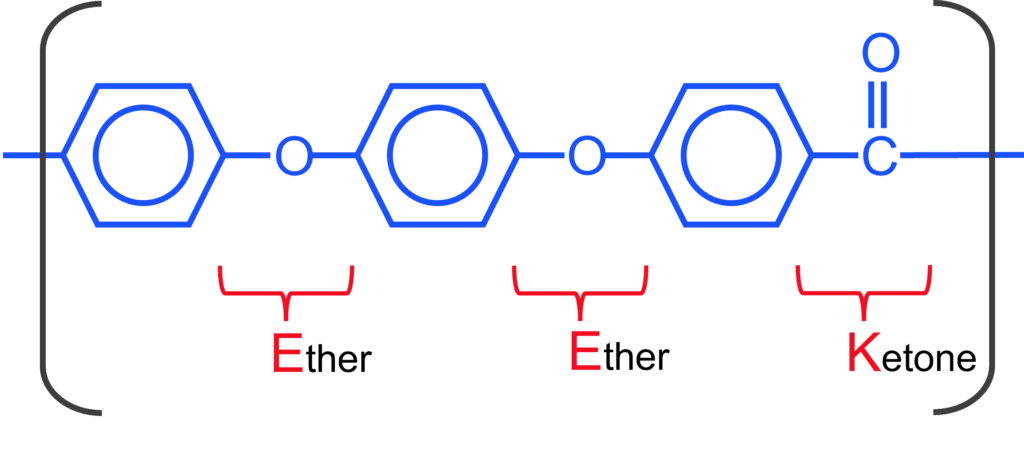
PEKK
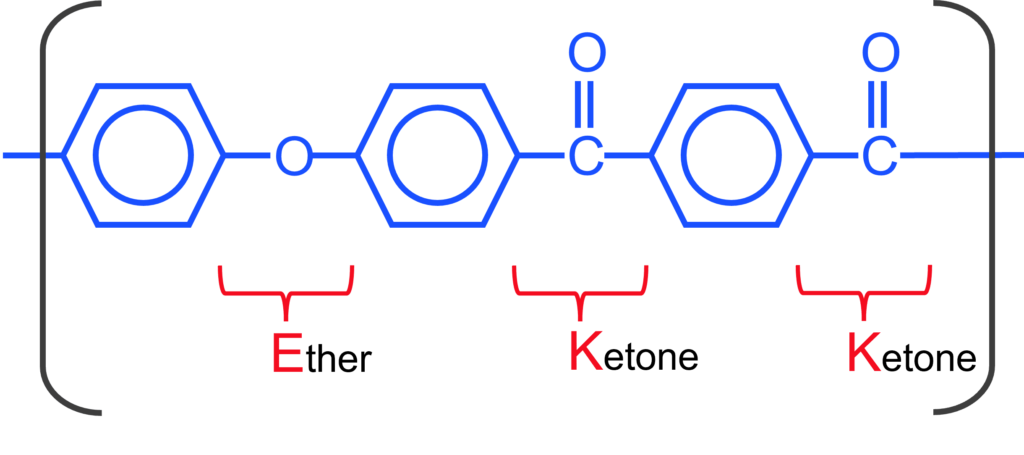
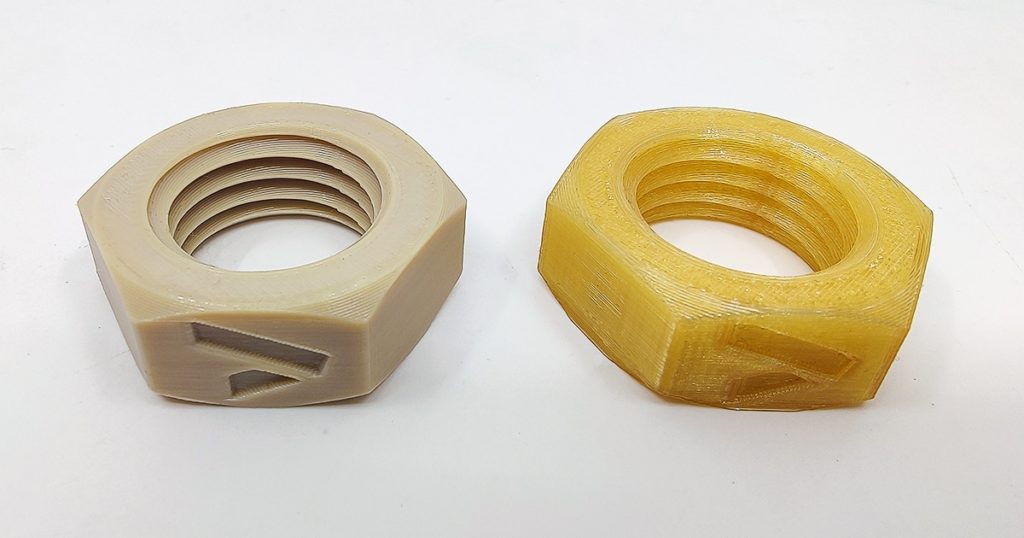
Here lies the true benefits of PEKK for processability. By controlling the co-polymer ratio, you can slow down the crystallization rate such that warpage is minimized during printing. For example, a ratio of 60/40 PEKK will form crystals slowly during printing. Alternatively, a ratio of 80/20 PEKK will form crystals rapidly and falls under the category of a semi-crystalline polymer blend.
By minimizing crystallization, the printed layers are more homogenous and the shrinkage between layers are not as significant as in PEEK. Therefore, printed parts have better dimensionality, interlayer weld strength and accuracy compared to their digitally designed counterpart. If you’re looking for a good balance between material properties and printability, you can find amorphous PEKK blends commercially which don’t crystallize at all during printing.
Conclusion
Throughout this article, we’ve learnt that PEKK offers better printability due to slower crystallization rates compared to PEEK. While the mechanical and thermal properties of PEEK are arguable superior to PEKK, warping in printed PEEK parts can be significant due to the rapid crystallization rate. Depending on the application, both polymers provide a strong case for replacing metals and printers such as the AON M2+ are capable of manufacturing PEEK and PEKK components.
Recommended settings for PEEK and PEKK printing
PEEK | PEKK | |
Extrusion Temperature (°C) | 400-450 | 320-360 |
Bed Temperature (°C) | 190-210 | 120-160 |
Chamber Temperature (°C) | 135 | 135 |
Printing speed (mm/s) | 10-40 | 20-40 |
Achieve New Levels of Part Performance & Throughput
3D print the world's highest performance polymers - bigger, faster, and stronger than ever.