3D Printing with PEEK, PEKK, & ULTEM™
Join AON3D's 3D printing application and materials experts for a 30-minute session that covers all the key information
Advancements in additive manufacturing polymers are closing the gap between 3D printed part properties and bulk material properties. The addition of chopped carbon fiber (CCF) to filaments, such as Polyamide, is one method that has enabled manufacturers to achieve better mechanical properties. In this article, we discuss the benefits of chopped carbon fiber and why some 3D printers, such as the AON M2+, are able to print 2X stronger and stiffer parts compared to others.
Benefits of Chopped Carbon Fiber-Filled Nylon
Polyamides (PA), or Nylons, are a family of affordable engineering-grade 3D printing polymers known for exceptional mechanical and thermal properties. Polyamides also have a high baseline ductility and since carbon fibers reduce ductility, PA is an ideal material to add carbon fiber reinforcement. By adding CCF reinforcement, manufacturers are able to increase final part strength by up to 115%, tensile modulus by 530%, and stiffness by nearly 300%.
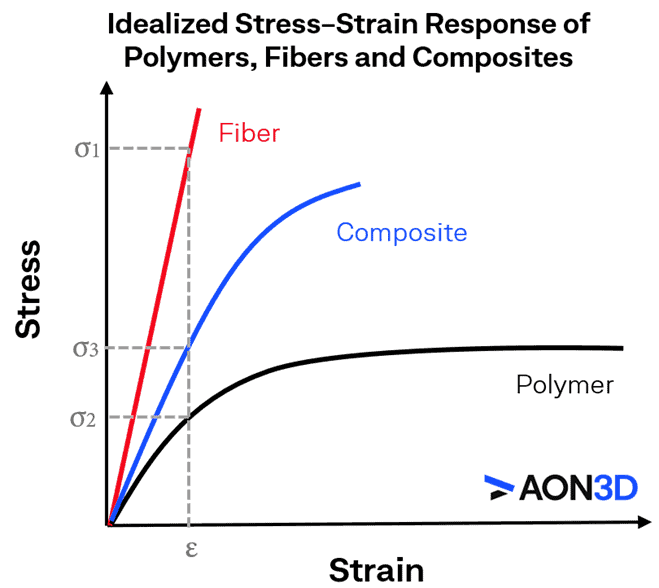
Unfortunately, Polyamides are also known to possess a high shrink rate which leads to warping and cracking during the 3D printing process. Thankfully, the inclusion of chopped carbon fiber reduces thermal expansion and shrinkage, improving ‘printability’ and the dimensional accuracy/stability of printed parts.
It is important to note, as seen in the following section, proper hardware and processing conditions greatly influence the mechanical properties of printed parts.
Comparing the Market
TDS Review & Analysis of Unfilled and CCF Nylon Filaments
Property | Test Method | Open Market PA6 Copolymer |
Proprietary Nylon |
Proprietary CF Nylon |
Jabil PA 4535 CF |
---|---|---|---|---|---|
wt.%, Carbon Fiber | – | 0% | 0% | 15% | 35% |
Tensile Strength (MPa) | ASTM D638 | 55 | 51 | 40 | 88 |
Tensile Modulus (GPa) | ASTM D638 | 1.9 | 1.7 | 2.4 | 10.6 |
Flexural Strength (MPa) | ASTM D790 | 76 | 50 | 71 | 118 |
Flexural Modulus (GPa) | ASTM D790 | 2.05 | 1.4 | 3 | 5.4 |
Price (USD/kg) | – | $77 | $193 | $215 | $120 |
Above, we analyze the TDS of several nylon filaments, filled and unfilled, to see how much the chopped carbon fiber influences final part properties and how they compare to each other. Of note, parts printed in Jabil PA 4535 CF yielded over double the strength, 5X tensile modulus, nearly double the stiffness, and at almost half the cost compared to parts produced on a prominent carbon fiber 3D printer with a proprietary carbon fiber-filled nylon.
While further testing would be needed to provide complete mechanical result interpretations, a 2022 study from AON3D’s Yahya Abderrafai, Ph.D. found that heated build chambers increase tensile modulus and ultimate tensile strength in 3D printed parts, even in lay-flat specimens. While the mechanics of filament cohesion are still being studied, one theory for the phenomenon is that the heated build chambers increase interfacial strength while reducing porosity. In our TDS comparison, variations in carbon fiber load, length, and weight put aside, disproportionate reductions in the proprietary carbon fiber material’s mechanical performance are inferred to be caused by specimens being printed in an unheated build volume on an unheated build surface.
Achieve New Levels of Part Performance & Throughput
3D print the world's highest performance polymers - bigger, faster, and stronger than ever.